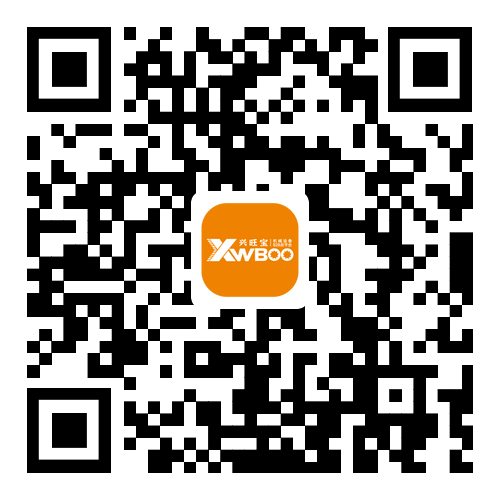
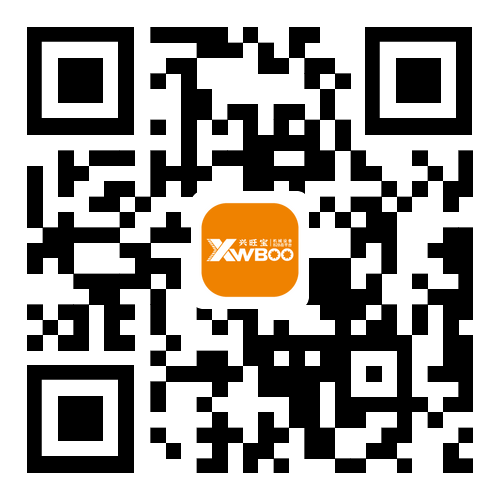
参考价 | 面议 |
产品详情
01-背景
1.1当前企业面临的问题和挑战
项目在前期概念规划阶段未对方案进行全面的评估与分析验证。
设计部门与工艺部门工作缺乏同步,只有在设计部门发布数据后,工艺才能开始工艺设计。
设计中静/动态干涉问题,设计不合理,工装不满足生产等问题发现的过晚,导致成产阶段问题集中暴露,影响生产。
工艺部门与设计部门协同效率较低。
1.2 工艺设计工作未能实现技术转变
未能真正意义的与产品开发同步,进行三维化的工艺审查,工艺编制基于BOM,文档,采用传统的手段进行,不具备全面的工艺检验技术手段。
02-虚拟装配项目实施目标
基于三维模型进行模型审查,干涉、可加工、结构可装配的问题,并将研发的设计问题进行反馈与问题归零闭环。
基于三维模型的工序及工位资源规划。
对装配过程中的装配路径、空间干涉、工位资源、人员操作可达与可视性的仿真验证。
工艺输出装配可行性视频。
03-解决方案
解决方案基于达索3DE平台,可以实现设计部门与工艺部门的数据的连续性,工艺部门与设计部门进行高效的协同设计,乃至后续可以延伸到生产和运维中进行高效协同。
3.1 获取产品模型
由于工艺部门与设计部门使用同一平台开始设计工作,所以数据的获取直接从3DE系统获取产品三维模型,产品工程BOM结构就在三维三维模型的结构树上,BOM信息与模型一一对应,工艺部门就基于三维模型获取产品的制造要求信息。
3.2 三维环境下基于模型的评审(面向装配)
工艺部门与设计部门针对模型的评审直接使用带有三维标准信息的MBD模型进行审查,根基审查的结果工部门与设计部门通过集成在CATIA模型上的审查清单,逐项的对审查设计的问题进行筛查;并根据审查的筛除的结果创建评审场景,进行标注注释,附加语音,图片,文字的说明。
3.3 创建问题反馈及跟踪记录清单
完成审查后,通过干涉检测与分析,在3DE系统内实时实施的记录分析过程发现的各类问题,由系统自动推送到产品开发部门负责人;对于各类发现的问题,进行单一的追踪和管理,最终落实为系统内各类产品数据的设计及有效性变更;通过数据接口,将问题导出发送给其它系统用于问题分享;整个问题处理的流程的状态,从提单到关闭,以及关闭后的存档,全部可查。
3.4 基于三维模型的装配过程模型重构
依据设计部门的产品工程BOM(EBOM)结构,完成符合生产制造过程物料BOM结构创建,结合总体工艺路线,完成制造过程物料的信息维护。
3.5 基于三维模型的装配工序规划
依据工艺部门重构好的产品制造过程物料结构,再结合完整工艺路线的定义创建工艺BOM(PBOM)结构。在创建工艺路线过程,系统实施监控物料和路线的逻辑关系,并以三维缩略图的形式可视化显示在每个工序的托盘上,可以直接在路线上显示零件的三维图纸信息。
3.6 基于三维模型的工艺过程虚拟装配验证
依据编制的制造过程工艺BOM (PBOM)结构,进行制造可行性分析。系统自动生成工序零件的状态,快速的开展包含装配仿真、工具工装可行性等一系类制造可行性分析,装配路径可以由系统自动计算一条不干涉轨迹,可以手动定义轨迹。
3.7 创建问题反馈及跟踪记录清单
通过虚拟装配的仿真与分析的结果,将问题分类处理,是工艺路线问题还是模型设计问题,还是工装问题,将问题创建问题清单,在3DE系统内实时实施的记录分析过程发现的各类问题,由系统自动推送到产品开发部门。
对于各类发现的问题,进行单一的追踪和管理,最终落实为系统内各类产品数据的设计及有效性变更。
通过数据接口,将问题导出发送给其它系统用于问题分享;整个问题处理的流程的状态,从提单到关闭,以及关闭后的存档,全部可查。
3.8 基于三维模型的作业工具及工装规划
在3D中,基于三维工厂模型进行各类工具、工装、设备的管理;通过系统提供的设备资源类型,对现场的各类工具、工装、设备进行分类定义,结合产品模型,将产品模型布局虚拟的产线上,定义产品在工厂中实际生产的环境,进行模拟生产,验证现有工装设备是否能满足产品生产。
04-总结
通过基于三维数据的虚拟装配的解决方案,打通产品研发与工艺设计之间的数据断层,使得工艺设计下产品开发阶段就进行设计,工艺与设计的进行高效协同,从而使问题能够提前暴露,在设计阶段将问题解决。节省生产制造的金钱成本和时间成本。在运营维护上对于易损耗件的更换可以提前进行优化设计。